What variables affect the measurement of plastic color?
Variables in Plastic Color Measurement Using a Spectrophotometer
Accurate color measurement is critical for manufacturing plastic products. Color is typically measured with a color spectrophotometer that captures the light reflected off or transmitted through an object and quantifies it reproducibly. This measurement can be affected by variables such as the color scale, the type of light source (i.e., illuminant), the viewing or “standard observer” angle, the geometry of the measurement device, the sample preparation, and the sample presentation. These conditions are typically specified for a measurement to create consistency and comparability. Another variable that affects the measured color of a polymer is temperature. The phenomenon of color change due to temperature is called thermochromic.
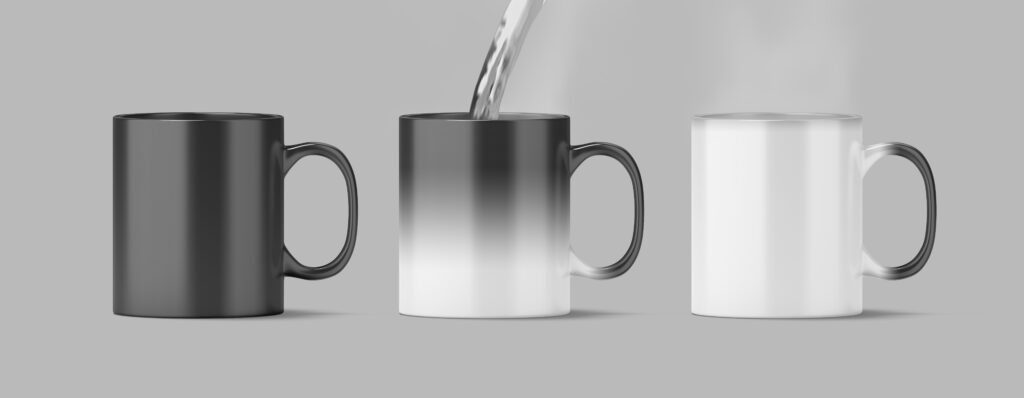
To understand how spectroscopy measures color, go to Equitech’s Knowledge Center to read about color measurement and how a spectrophotometer works.
How does temperature affect the color measurement?
Thermochromism of some colorants can result in a dramatic color change, such as a “magic” cup that changes from black to white when filled with a hot liquid. For other colorants, the color change due to temperature is not as significant but could still cause a sample to measure outside the color specification limits. To prevent this shift, labs typically control the ambient temperature of the environment and ensure that a sample is cooled to ambient temperature before measuring.
When measuring color with an in-line spectrophotometer with a probe inserted in the melt, the plastic melt temperature will affect the color appearance. However, correlations can be developed to correct the thermochromic effect in polymers. The current practice is to use a thermocouple placed in the die to obtain an approximation of the melt temperature in these equations.
How do you set a color specification for in-line measurement with a spectrophotometer?

Even with calculations to correct the thermochromic effect, an in-process L*, a*, and b* color value will likely differ from the same sample measured by a lab spectrophotometer because multiple other variables also affect these measurements. Since product color specifications are set using values measured in the lab, it is necessary to correlate lab-tested samples with in-process tested samples to select the in-process specifications for L*, a*, and b*.
Experiments run by Equitech demonstrated that, for a process running in a steady state, a correlation between the lab and process color could be determined for a specific polymer compound. Once the target in-process L*, a*, and b* are determined, the in-line process spectrophotometer can control the process to that target. Read “In-Line Color Monitoring of Plastics Compounds” in Equitech’s Knowledge Center to learn more about in-line process control using real-time color data.
Industry 4.0 quality control of plastics color
Real-time data will be required as the plastics industry adopts Industry 4.0 protocols and moves to greater process automation. In-line color measurement systems monitor color continuously to provide real-time data for process and product control.
Equitech manufactures opto-electronic solutions for in-line process measurements. For example, Equitech’s In-line Process Spectrophotometer (IPS) measures color in-line in real-time, directly in the polymer melt. Equitech’s EquiColor software displays L*, a*, and b* values and can activate an alarm if the measurement exceeds the specification range. These real-time data can also be used in closed-loop control for a more efficient, automated process that reduces scrap and produces a higher-quality product. To read more about how the EquiSpec IPS is used, for example, in recycled plastic compounds, see the Knowledge Center blog: “How to Control Quality of Recycled Plastic Compounds Using In-Line Color Measurement.”
Contact Equitech’s experts to learn how an in-line process spectrophotometer can benefit your operation.